A Detailed Guide on How to Conduct Quality Inspections and Supplier Evaluations
By: ExactureFeb 02, 2023
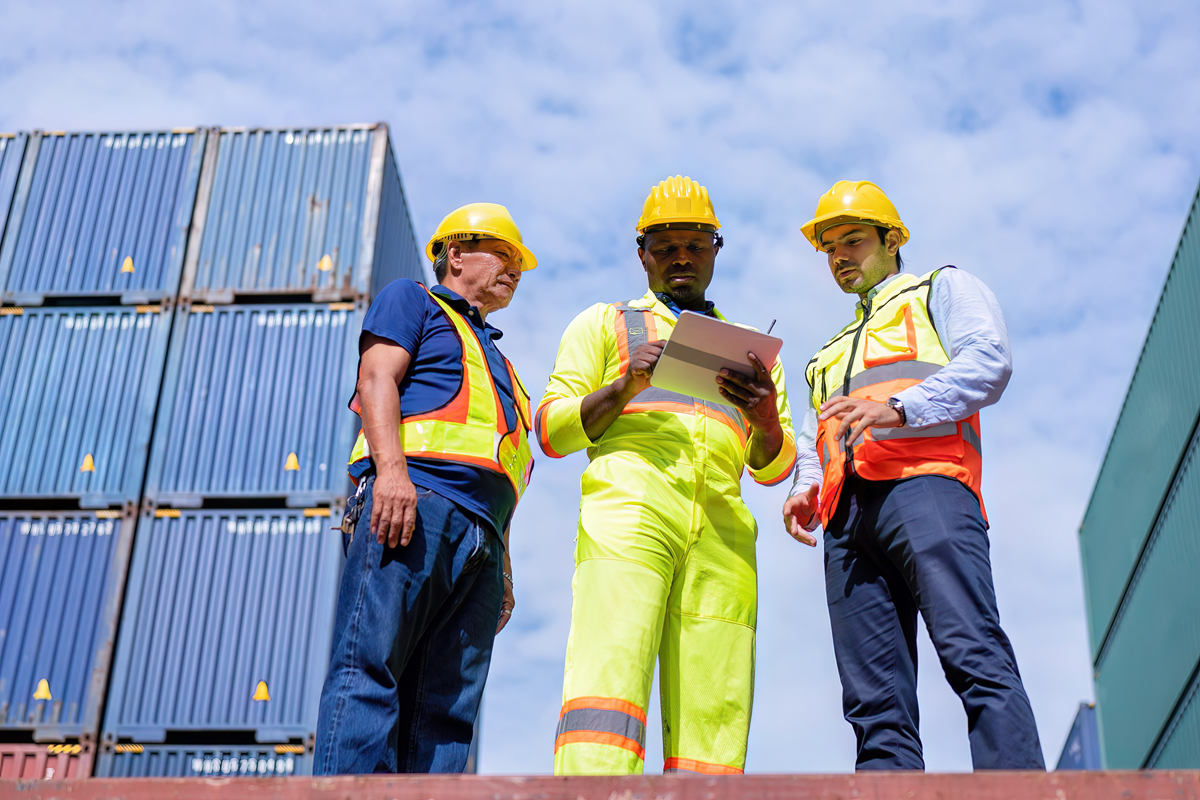
Conducting quality inspections and supplier evaluations are critical steps in maintaining the overall quality of products and services. These inspections and evaluations help organizations to identify areas where improvements are needed, and to take action to make those improvements. In this blog post, we will provide a detailed guide on how to conduct quality inspections and supplier evaluations, and how a Quality Management Software can improve the inspection and evaluation process.
Quality inspection
The first step in conducting quality inspections is to establish a set of inspection criteria. These criteria should be based on industry standards, as well as the specific requirements of the organization. The criteria should be clear, measurable, and relevant to the product or service being inspected.
Once the inspection criteria have been established, the next step is to conduct the inspection. This should be done by a trained inspector or someone internally who is familiar with the product or service being inspected. The inspector should use a checklist to ensure that all of the inspection criteria are being met. The inspector should also take detailed notes and photographs to document any issues that are found.
After the inspection is complete, the inspector should compile a report that summarizes the findings. This report should include a description of any issues that were found, as well as recommendations for how to address those issues. The report should be shared with the relevant parties, such as the supplier, the quality control department, and the management team.
Supplier evaluation
The next step is to conduct supplier evaluations. This process involves assessing the performance of suppliers and identifying areas where improvements are needed. The evaluation should be based on a set of criteria, such as delivery performance, product quality, and responsiveness to customer needs.
After the supplier evaluation is complete, the organization should take action to address any issues that were identified. This may include working with the supplier to improve their performance, or finding a new supplier.
How to improve your quality inspection process?
One of the key ways that a Quality Management Software can improve the inspection and evaluation process is by automating data collection and analysis. Exacture can be used to collect data on various aspects of the organization’s operations, such as product quality, production processes, and supplier performance. This data can then be analyzed to identify patterns and trends, which can be used to identify areas where improvements are needed.
Another way that software, like Exacture, can improve the inspection and evaluation process is by providing tools for monitoring and tracking progress. It can be used to monitor progress on continuous improvement initiatives, and to track the results of those initiatives. This can help organizations to see the impact of their efforts, and to make adjustments as needed.
In conclusion, conducting quality inspections and supplier evaluations are critical steps in maintaining the overall quality of products and services. A software based Quality Management system can improve the inspection and evaluation process by automating data collection and analysis, providing tools for monitoring and tracking progress.
Organizations that are looking to improve their overall effectiveness should consider booking a 15-minute preview. We’d love to hear from you and to show you how we can make a dramatic difference in your supply chain process. Ask us about our pilot programs where we outline a quick and efficient way to get started, with little to no financial risk to our partners.